The SVP Bombarding A.C. Milliamperes Meter
is a completely self contained unit with all
electrical connections enclosed within a safe,
PVC meter housing.
Unlike rectified meters, the SVP Bombarding A.C.
Milliamperes Meter is based on a Simpson® True
RMS Iron-Vane meter, which provides an
accuracy of ± 2% deviation from the actual value
@ 60 Hz.
(See comparison) This eliminates the
guesswork normally associated with using a
lesser quality instrument (regardless of what
suppliers sell them for) and assures the
processing technician that the proper amount of
current is being applied at the appropriate times
throughout the processing procedure.
|
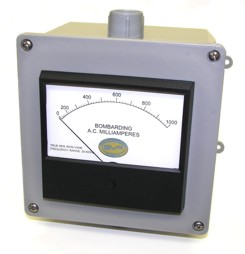 |
The large 4˝” meter face allows the instrument to be mounted
safely away from the operator while still providing at-a-glance
information, and the 0-1,000 scale range is ideally suited for
neon work where the maximum current applied is typically less
than 1,000 mA for even the largest units. A 0-2,000 range meter
of the same type is available by special order for shops
involved in manufacturing large diameter, high current Cold
Cathode Lamps.
SUMMARY:
A Bombarding A.C. Milliamperes Meter is one of the four
instruments essential for proper luminous tube processing. This
instrument monitors the level of bombarder current in
milliamperes that is generated by the bombarder, through the
tube being processed. It is necessary to accurately monitor the
current for the tubing and electrode sizes used to ensure that
the right amount is applied at the appropriate time. To do
otherwise may cause damage to the electrodes, fluorescent
coating inside the tube and adversely affect the glass
structure. Therefore, it is desirable to use a True RMS
Iron-Vane meter, which is considerably more accurate than a
rectified meter.
Too high of a bombarding current during the first stages of
processing may damage the phosphors in coated tubing,
particularly in a moisture laden tube. This damage and loss of
efficiency reduces the initial light output of the finished tube
and may lead to premature discoloration and darkening in
fluorescent tubing. High currents for extended time may create
hot spots in the glass tube, particularly in tight bends. This
may cause the glass to deform to some extent and induce adverse
stress points within the glass structure. Excessive current will
also damage the electrodes. “Sputtering” is usually the damage
that is first noticed. Sputtering reduces the life of the
electrode and therefore the tube and can cause discoloration
near the electrode, both in clear glass and coated tubing. This
situation is particularly troublesome in mercury tubes as the
discoloration may spread for some distance into the tube.
Further, the electrode wires where they attach to the back of
the metal shell may become brittle causing the shell to fall off
the wires. The damage and resulting tube failure may not be
evident until the tube has been in service for some time.
Too low of a current can make the bombarding process take too
long and not allow the glass and electrodes to reach the proper
temperature. Although a slow “cook” time is more desirable than
a fast one, if it takes too long the phosphors and electrodes
may be damaged from extended exposure to high currents. While it
is necessary to get the electrodes’ metal shells a bright,
incandescent, light shade of orange (like an illuminated pumpkin
orange) the entire length of the shell, only the minimum amount
of current to accomplish this should be used and it should be
accomplished in a reasonably short time. Therefore, bombarding
current must be monitored accurately and the higher currents
required to fully process the electrodes should only be used for
a few seconds at the end of the bombarding procedure. |